The droplet expulsion bell comes in directly after the ampoule filling operation.
Fully automated, this machine is matched to the throughput speed of the filler.
This complementary module fits perfectly into a fine-tipped ampoule filling line.
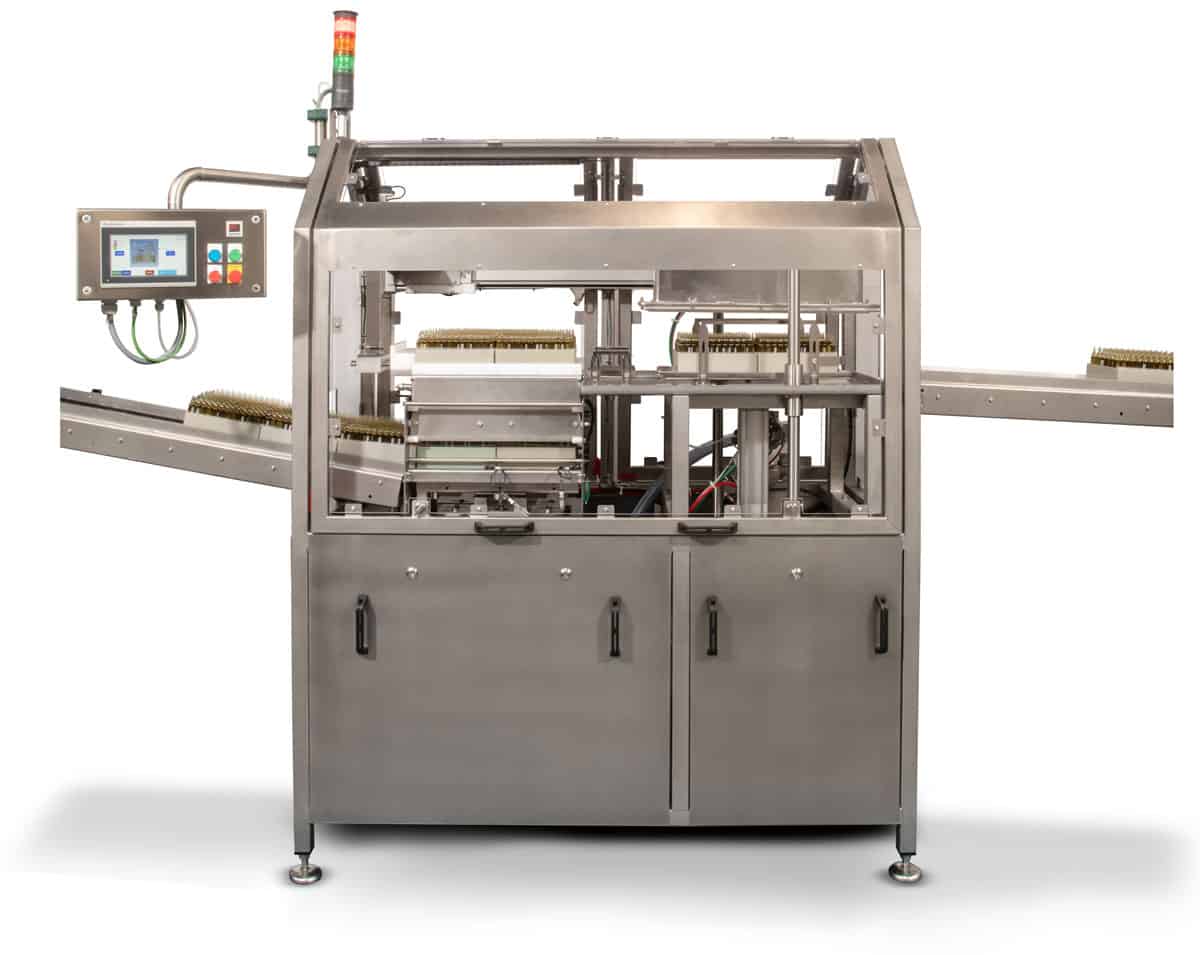
Capacity
Up to 300 crystallizing dishes per hour (measured on mains water)
Customizable filling line
With four filler models and a wide range of complementary modules, each production line is precisely matched to the customer’s specific needs.
Small footprint
Ergonomic and compact, VACFILLER machines can easily be integrated into all types of laboratory.
Compliant with BPF and FDA specifications
The whole of the VACFILLER range complies with BPF (French good practice in manufacturing) and FDA requirements for pharmaceutical industry products and dietary complements.
What is the purpose of the droplet expulsion bell ?
The Bell eliminates any droplets of product that remain on the tip of the ampoule after it has been filled, greatly facilitating the sealing weld operation.
This machine is suitable for liquids that are difficult to eliminate, such as oils or other viscous products.
It fits in easily between the filling and sealing modules of an ampoule filling line.
How does it work?
With a standard construction based on Vacfiller 300, this machine loads two crystallizing dishes into the inspection tank.
The droplet expulsion operation then takes place either by vacuum or by pressurization.
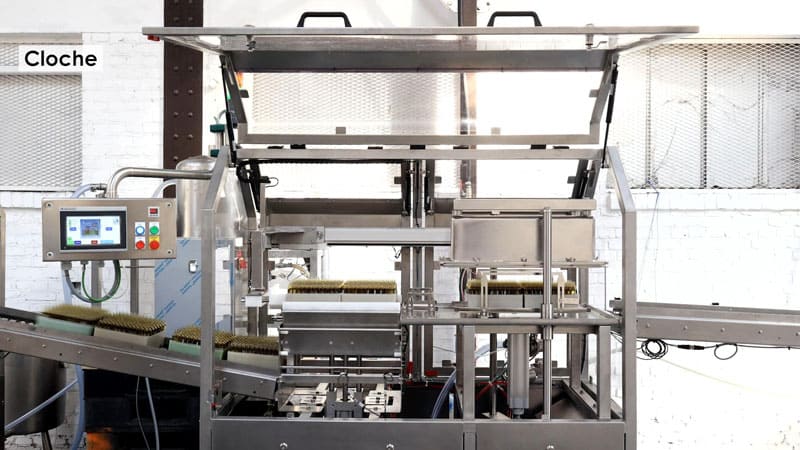
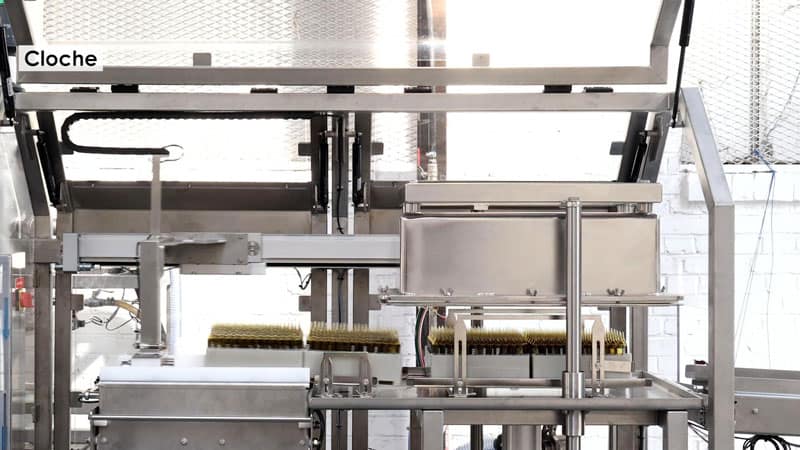
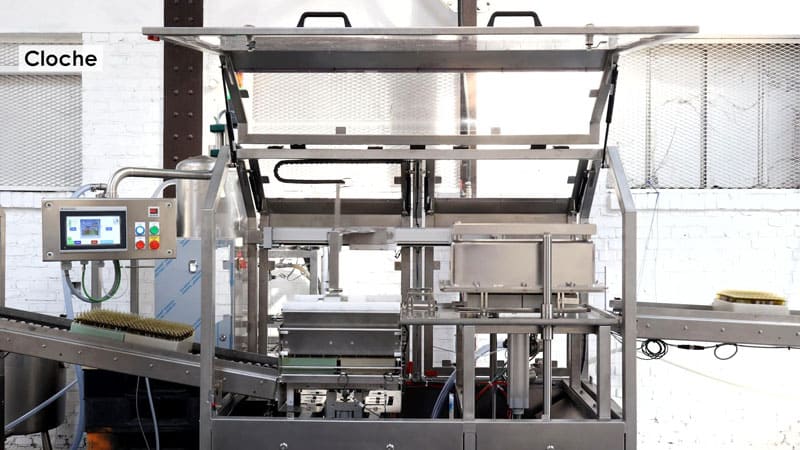
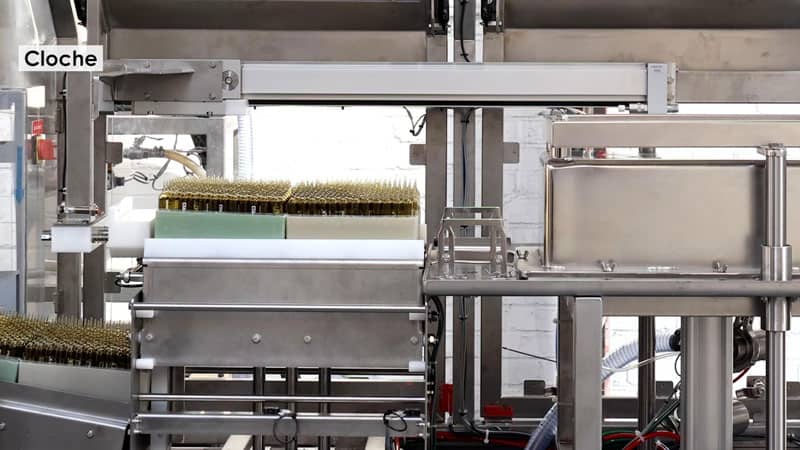
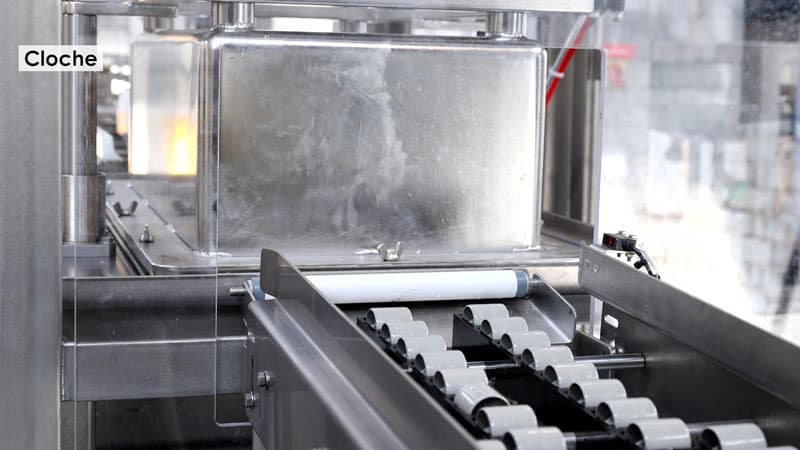
Designed to rid the ampoule’s fine tips of all residues !
With its simplicity of use and studied ergonomics, the droplet expulsion bell quickly eliminates all residual liquid that might be left on the ampoule tips.
- Input feed from the Filler module by in-line gravity conveyor ;
- Standard stainless steel construction based on Vacfiller 300 ;
- Good accessibility and easy cleaning ;
- Compatible with all ampoule formats without adjustment ;
- Modification and recording of settings for different cycles ;
- Addition/modification of recipe programs for various products ;
- Especially effective when sealing oily substances ;
- Assisted troubleshooting from the user interface ;
- Recording and repeatability of different settings ;
- Bypass operating mode possible ;
- New range of long support-life PLCs.
Installation prerequisites
- 220V 50Hz power supply ;
- Filtered compressed air at a constant 6 bar ;
- Vacuum ;
- Effluent discharge connection.
Optional extras
- Development of custom programs for your specific products ;
- Droplet expelled by vacuum ;
- Liquid ring vacuum pump with partial water recycling ;
- Liquid ring vacuum pump with total water recycling + chiller unit for almost zero water consumption ;
- Droplet pushed back in under pressure, with or without inert gas ;
- Free choice of automation brand.
A bespoke, upgradable production line with many advantages
The VACFILLER range can package ampoules from A to Z in record times. There are many advantages in all of the machines, not the least of which is a quick return on investment.
VACFILLER machines fill ampoules with extreme accuracy, guaranteeing reliability and quality.
Ergonomic and intuitive, VACFILLER machines have a short learning curve thanks to their simplicity of use.
VACFILLER modules are standard design machines. Maintenance is therefore performed using commonly available parts.
By filling their ampoules in-house, laboratories maintain full control over the packaging chain, especially on quality and lead-time.
Each model meets a well-defined requirement, ensuring perfect productivity, and accordingly a very short payback time.
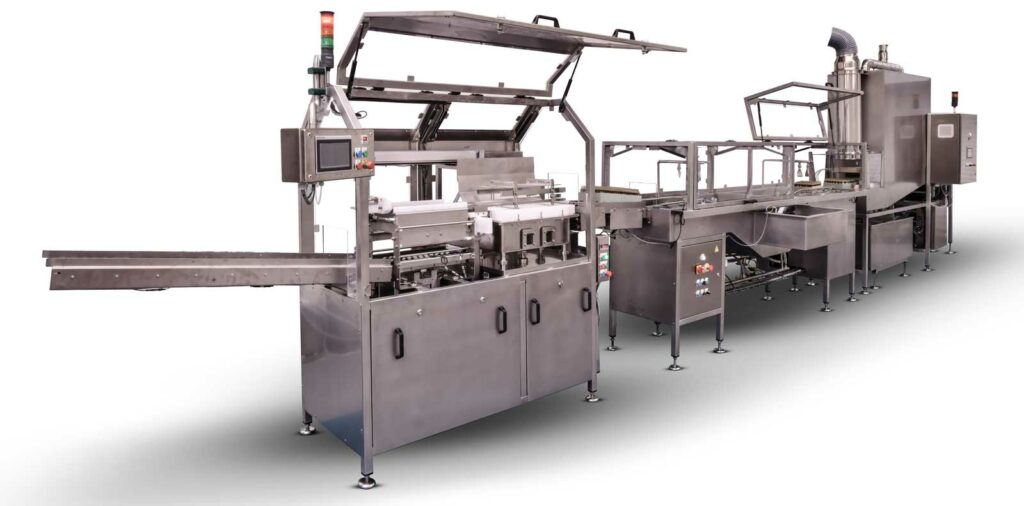